
WIND TURBINE BLADES
The goal of this project was to work with a group of Mechanical and Electrical engineering students to design and optimize blades for a miniature wind turbine. The turbine will be designed to efficiently charge two AA batteries under 2 hours.

AIRFOIL SELECTION
The first step for our team was to decide on a proper airfoil to use for our design. After researching numerous profiles, we decided on using the SG6043 airfoil which is specifically designed for wind turbines. Lift and Drag data was procured using XFOIL, a software that analyzes airfoils.

INITIAL DESIGN
After analyzing the data from XFOIL, the geometry of the blade was determined using theoretical values for angle of attack and camber. The design showed to be too thin due to high curvature, so linearization of this design was done to create a more desirable blade.
FINAL DESIGN

MANUFACTURING
Through team consensus, carbon fiber was used to fabricate the blades due to the materials high fatigue resistance and exceptional strength. The blades were first 3D printed using PLA, then wrapped with the carbon fiber composite using a vacuum bagging method.

WIND TUNNEL TEST
Due to the constraints of the wind tunnel at WSU, the designed blades were trimmed at the ends to properly fit in the test section. Power output was recorded at various speed settings of the tunnel.
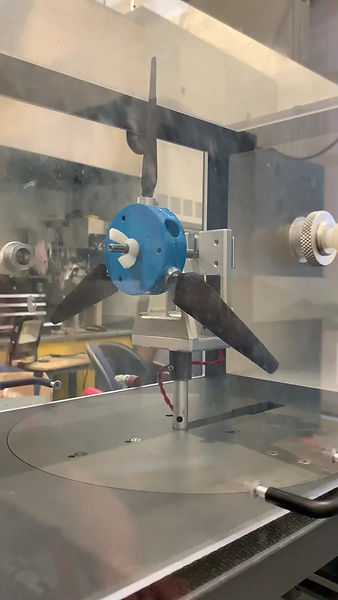

RESULTS
The carbon fiber blades that were designed by my team was able to effectively recharge 2 AA in 1 hour and 30 minutes. This project has taught me about the vacuum bagging process and using a wind tunnel to simulate real life conditions for wind turbines.